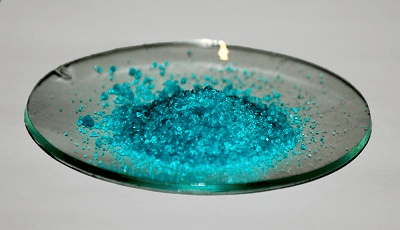
Application Examples in electroplating industry: Removing Iron Impurities from Nickel Sulfate Solution
Background
In the electronics and semiconductor industries, the purity of nickel plating solutions is crucial. Excessive iron impurities in nickel sulfate plating solutions can degrade the quality of the coating, reducing conductivity, corrosion resistance, and potentially causing defects during the plating process. Therefore, effective removal of iron impurities from nickel sulfate solutions is necessary.
Using Our Company's MC900 Chelating Ion Exchange Resin to Remove Ferric ion
Choosing the Right Chelating Resin:
- Select a chelating resin with high selectivity and adsorption capacity for iron ions (Fe²⁺ or Fe³⁺). Commonly used chelating resins include IDA (Iminodiacetic Acid) or EDTA (Ethylene Diamine Tetraacetic Acid) resins, known for their excellent selectivity towards iron ions.
Resin Pre-treatment:
- Before use, the chelating resin needs to undergo pre-treatment to ensure it is in optimal working condition. Pre-treatment typically involves repeated washing with acid (such as dilute hydrochloric acid) and base (such as sodium hydroxide) solutions to remove impurities from the resin.
Column Packing and System Preparation:
- Fill the pre-treated chelating resin into an ion exchange column. Ensure an even resin bed to avoid air bubbles and gaps.
- Connect the inlet and outlet liquid lines, and prepare circulation pumps and storage tanks.
Processing the Electroplating Solution:
- Pass the nickel sulfate electroplating solution containing iron impurities through the ion exchange column packed with chelating resin at an appropriate flow rate.
- Control the flow rate and contact time to ensure effective adsorption of iron ions. Multiple cycles of processing may be required to achieve the desired purity.
Monitoring and Analysis:
- Monitor the concentration of iron ions in the treated electroplating solution using detectors or laboratory analytical equipment (such as Atomic Absorption Spectroscopy or ICP-MS) to ensure it is reduced to the required level.
- Adjust processing conditions as needed or repeat the process until the desired purity standards are met.
Regeneration and Maintenance:
- After the resin becomes saturated with adsorbed iron ions, regenerate it. Regeneration typically involves using acidic solutions (such as dilute hydrochloric acid) to elute the adsorbed iron ions, followed by rinsing with deionized water.
- Regularly maintain and regenerate the resin to extend its lifespan and maintain treatment effectiveness.
Specific Results:
Through this process, iron impurities in nickel sulfate electroplating solutions can be effectively removed, ensuring high purity of the electroplating solution and thereby improving the quality of the electroplated layers. Below is a comparison of iron ion concentrations before and after chelating resin treatment:
- Before Treatment: Iron ion concentrations may be in the range of several hundred ppm (parts per million) or higher.
- After Treatment: Iron ion concentrations typically decrease to below 10 ppm, and even as low as 1 ppm, depending on specific requirements.
Conclusion
The application of chelating ion exchange resin in the electroplating industry, particularly for removing iron and other metal impurities from electroplating solutions, is a critical method to enhance plating quality and purity. In the electronics and semiconductor industries, this method ensures the conductivity, corrosion resistance, and overall performance of plated layers meet high standards of purity and quality.